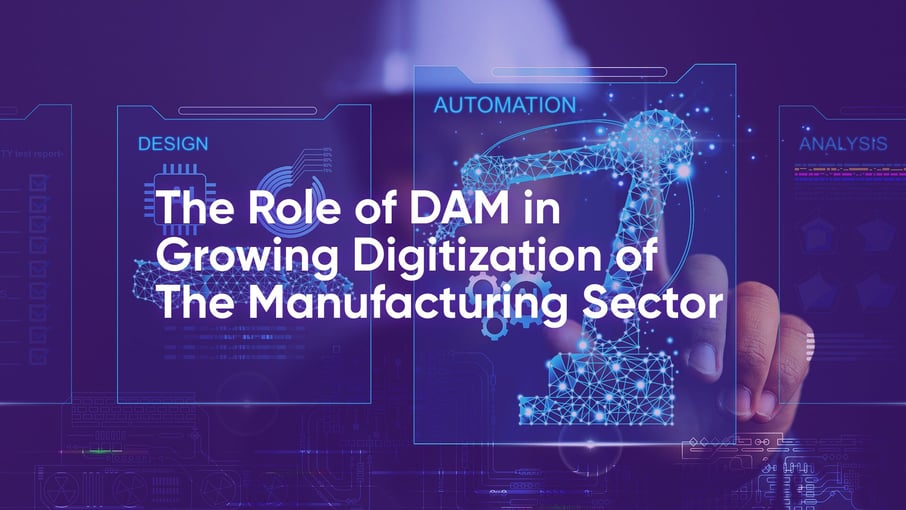
Industry 4.0, or the next chapter in the digitization of the manufacturing industry, is where it all began. It can be considered the building block behind the digitalization of asset-intensive industries like manufacturing, which then fueled automation, data-driven connectivity, analytics, and improved man-machine interaction.
In other words, digitization (which was followed by digitalization) has emerged as the reason behind supercharging operational efficiency, bettering employee experience, and shaping flawless customer journeys. A vital component for manufacturers in all of this is to address their digital asset consistency, visibility, governance, and integrity, mainly due to the growing complexity of digital data. And that is where the adoption of systems like digital asset management (DAM) emerges. This insight offers a distilled picture of DAM’s significance for manufacturers regarding controlling, connecting, and future-proofing themselves in the context of Industry 4.0.
The Need for DAM in the Manufacturing Sector
The purpose and intent behind managing digital assets are well-established in manufacturing. While the aim is primarily to do with handling complicated product portfolios, numerous market routes, multiple global locations, diverse customer segments, and distribution channels—the intent is to do away with inconsistencies, siloed processes, and discrepancies while efficiently handling scattered, disparate digital asset data via bringing it under one single digital asset repository. For manufacturers, the significance of DAM is also about driving value through better governance, management, and accurate versioning of digital assets to ensure that they reach the right people at the right time. Moreover, a DAM system facilitates enterprises to transfer files, improve productivity (through automated workflows), and strengthen reputation and influence through digital assets. Once the reliability of digital assets is established across channels to power engaging online and offline customer journeys, it gets easier for asset managers to maintain operational resilience, respond quickly to market changes, launch products in newer geographies, and adapt to evolving business strategies vis-à-vis operations and distribution.
Challenges for the Manufacturing Industry When Implementing a DAM System
Manufacturers often find themselves surrounded by several unique challenges when it comes to implementing a DAM system. Some of the common challenges are:
- Volume of Data: Managing vast amounts of digital assets (like product images, technical drawings, animations, presentations, documentation, logos, marketing collateral, etc.) efficiently within a DAM system requires not just meticulous planning but skilled resources, which many manufacturers may lack.
- Integration with Existing Systems: Integrating the DAM system with their existing software systems, such as customer relationship management (CRM), enterprise resource planning (ERP), and product lifecycle management (PLM) systems, can be complex and require custom development work.
- Security and Access Control: Manufacturing companies often deal with sensitive data, including proprietary designs and manufacturing processes. Since ensuring the security of their assets and controlling access for different user groups is critical, it can postpone their implementation decisions.
- Metadata and Tagging: Properly tagging and adding metadata to assets is crucial for efficient asset retrieval. However, it can be time-consuming and may require standardizing naming conventions and taxonomies. Many manufacturers may not have the resources for it.
- Training and User Adoption: Employees must be trained to use the DAM system effectively. Resistance to change and a lack of user adoption can also hinder successful implementation of DAM.
- Mobile Access: With many employees working remotely or in the field, ensuring that the DAM system is accessible and functional on mobile devices has gained increasing importance. Doubts of incompatibility can also affect implementation plans.
- Cost of Implementation: Implementing a DAM system can be a significant investment in terms of both software and hardware. Companies need to allocate the budget for deployment, customization, and maintenance costs.
How DAM Prepares Manufacturers for ‘Industry 4.0’
Industry 4.0, or the fourth industrial revolution, is being shaped by intelligent computers, where cloud technology, sensors, blockchain, advanced analytics, machine learning, AI, AR, VR, and robotics bring disruption never imagined before. Manufacturing is now fuelled by a vast volume and variety of information emerging in real-time from across geographies. There is an intermingling of technologies that is taking place involving systems, applications, and tools. And DAM is one of the systems that’s turning into a nerve center of digital assets. DAM mainly aids from the following perspectives:
1. Workflow Management
The workflow management capabilities of DAM allow business users to efficiently construct and modify the flow of work via intuitive, graphical drag-and-drop interfaces. The workflow structure can also be created as a loop, where the steps keep repeating. For example, when a graphic designer creates an asset, it gets reviewed by marketing and sales teams, goes back to the designer for any further changes, and finally enters the DAM system as the go-to version.
2. Asset Delivery
DAM ensures effective asset delivery so that only designated people can access specific assets. From providing asset libraries (that serve as customized portals offering curated collections of assets tailored to particular audiences) to integration with content delivery network (CDN) (for delivering large files or high-traffic assets) to improve asset delivery speed and reliability—DAM not only streamlines dissemination of digital assets but enhances collaboration and compliance.
3. DAM System Integration
DAM systems can effortlessly integrate with other tools and platforms, such as CMS, CRMs, ERPs, PLMs, email marketing software, supply chain software, and design tools. It allows for direct asset usage without manual downloads and uploads and can ensure seamless operations to ensure data consistency and synchronization. Industry 4.0 thrives on horizontal integration (production floor and supply chain) and vertical integration (vertical layers such as sales and marketing, quality assurance, R&D, etc.).
The Importance of Enterprise Metadata Management for Manufacturing
Enterprise metadata management is a foundational element that underpins manufacturers in several ways, starting with data visibility and accessibility. It ensures that data is appropriately categorized, labeled, and indexed, making it easier to locate and access whenever needed. Metadata management heavily contributes to data quality by applying standardized naming conventions, data definitions, and validation rules; clean and accurate data is essential for manufacturing processes.
Manufacturing organizations also deal with a lot of sensitive and regulated data, such as product designs, safety protocols, and compliance documentation. Metadata management supports data governance efforts by tracking data lineage, providing audit trails, and enforcing security and access controls. Besides, adequately managed metadata facilitates collaboration by ensuring all stakeholders can conveniently find and understand the data they need to work efficiently. Metadata management also contributes to better data analytics, as when data is properly labeled and categorized, it becomes easier to analyze trends, identify areas for improvement, and make data-driven decisions that can optimize manufacturing processes.
Overall, enterprise metadata management is instrumental in streamlining operations, enhancing decision-making, improving productivity, making enterprises better positioned to adapt to market changes, responding to customer demands, and innovating and gaining a competitive edge.
How Manufacturing Leverages DAM Through AI/ML and IoT
Digital Asset Management (DAM) aids various new-age technologies like AI, ML, and IoT that have emerged with Industry 4.0 and are likely to play a pivotal role in the future of digital assets, and manufacturers can use this to their advantage:
Machine learning (ML)
Machine learning algorithms can automatically tag and generate metadata for digital assets. This significantly speeds up the process of categorizing and organizing assets in the DAM system. ML can analyze user behavior and preferences within the DAM system to make content recommendations. Manufacturers can benefit from this by ensuring that designers, marketers, and other team members can quickly find the most relevant assets for their projects. ML models can also extract valuable information from images and videos. For instance, visual recognition algorithms can identify defects in manufacturing processes, assist in quality control, and monitor the condition of equipment and machinery.
Artificial intelligence (AI)
AI-powered search engines within the DAM system can understand natural language queries and retrieve assets accurately. For manufacturers, this means that employees can easily find product documentation, technical drawings, and rich media assets without being constrained by rigid search queries. AI can assist in the creation of marketing collaterals, product manuals, and related content. It can also help personalize content for specific customers or target audiences to improve customer engagement and satisfaction. AI can also analyze historical sales data and market trends stored in the DAM system to predict future demand for products. Manufacturers can use these insights to optimize production schedules and inventory management.
IoT (Internet of Things)
IoT devices, such as sensors and RFID tags, can be used to track physical assets, such as inventory, machinery, and products, in real time. Data generated by these devices can be stored in the DAM system, providing a comprehensive view of asset locations and statuses. IoT sensors can monitor manufacturing processes and quality control parameters. Alerts can be sent out when any deviations occur, and generated assets, such as inspection reports and images, can be stored in the DAM system for further analysis and audit purposes. Consequently, when maintenance predictions are made, the DAM system can automatically provide teams with necessary documentation and work orders to address issues proactively, reducing unplanned downtime and extending equipment lifespan.
What To Consider While Selecting a DAM System for the Manufacturing Industry?
Selecting a Digital Asset Management (DAM) system for the manufacturing industry requires careful consideration of specific industry needs, processes, and goals, such as:
- Identifying objectives: These could include improving asset organization, enhancing collaboration, ensuring compliance, or streamlining production processes.
- Assessing current assets: Taking stock of all digital assets present within an organization.
- Defining user requirements: Identifying the needs of key user groups that would use the DAM system, e.g., designers, engineers, marketing teams, etc.
- Integration needs: Evaluating how the existing systems and software currently in use can be seamlessly integrated with the DAM system.
- Budgeting: Outlining a clear budget for DAM implementation (including software licensing), customization, training, and maintenance costs.
- Compliance and security requirements: Considering industry-specific compliance standards or regulatory requirements to ensure the intended DAM system supports compliance needs.
- Scalability: It is crucial to examine the scalability of the DAM system if it can accommodate future growth and an increasing volume of digital assets.
- Usability and User Training: Analyzing the intuitiveness of the DAM interface, the quality of the training resources, and how fast the employees can be trained before they use it effectively.
Pimcore Use Case: DAM for Manufacturing
Pimcore helped a global automotive manufacturing brand by centralizing its digital asset management and simplifying asset sharing.
The organization is present in 60 countries and employs around 245,000 people globally. They wanted to centralize and manage data of about 45K products and maintain it in 40+ languages for dissemination in 50+ countries. They desired to have a flexible and robust system to cater to their current and future digital asset management needs.
Earlier, their product assets were scattered across several internal systems, lying with various users. Users were not able to share data and asset files (related to different products) with internal and external agencies. There was no central visibility of assets across the globe for local marketing. Due to this, the tracking of approved or rejected assets could not occur properly. Incorrect and inconsistent usage of assets was happening for marketing and other purposes between various country-specific teams. There was no control or visibility of local assets being created and managed.
Pimcore implemented a robust DAM platform to centralize product assets along with product information across multiple countries. Customized approval workflows were implemented to manage and control published assets. With Pimcore’s DAM platform, the required data could be easily filtered and shared with different user groups as well as with external users.
As a result, the accessibility of centralized assets to users across countries became easier. Asset sharing became highly convenient. Centralized teams could now create and manage assets locally and get enhanced visibility. This ultimately simplified the management of assets, leading to improved operations.